
MAKING KNOTWOOD
The beauty of wood,
the benefits of aluminum
UNIQUE SUBLIMATION
KNOTWOOD PROCESS
Knotwood’s unique sublimation process makes aluminum look and perform like real wood. Knotwood aluminum is technically designed to not only look good, but withstand the test of time. Knotwood is a sustainable, low-maintenance and high-quality building material. Knotwood’s true beauty doesn’t rest in its durability and aluminum capabilities, but rather in the natural beauty and timeless appeal of its lifelike wood finishings.

STEP ONE
EXTRUDING
KNOTWOOD
PROFILES
EXTRUSION
The process begins by heating the stock billet material. It is then loaded into the container in the press. A dummy block is placed behind it where the ram then presses on the material to push it out of the die. Afterward the extrusion is stretched in order to straighten it.
PAINT LAYERS
The next stage in Knotwood’s process involves powder coating. Electrostatic guns are used to make 80-120µ (microns) powder paint layer. Polymerization is performed afterwards by heating the profiles to 220 degrees Celsius for 30 minutes. The base coat that is applied is very durable and scratch resistant. This coat also serves as protection of the aluminum from external factors such as abrasion, corrosion, weather, humidity, and UV damage.
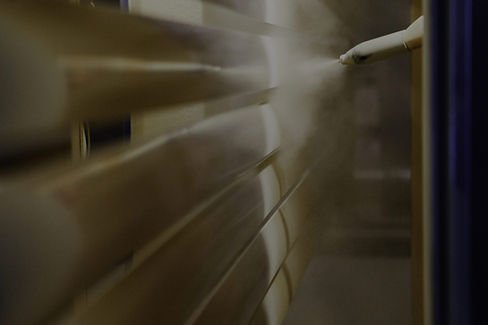
STEP TWO
POWDER COATING
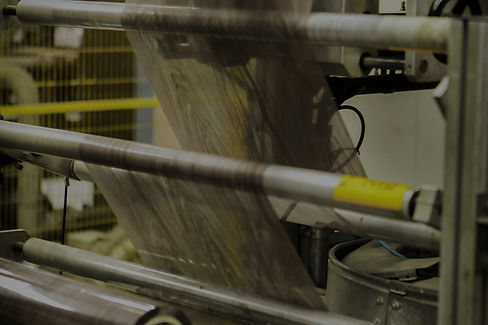
STEP THREE
WOOD
EFFECT
SUBLIMATION
The powder coated aluminum is wrapped in one of Knotwood’s many films and set on a conveyor system, then the air is vacuumed from the film around the aluminum. The conveyor transports the aluminum into the oven, under heat and pressure the film transfers the Knotwood image onto the aluminum.
KNOTWOOD BY THE NUMBERS
57
EXTRUSIONS
29
WOOD GRAIN COLORS
10
UNIQUE SYSTEMS
12
NATIONAL AWARDS